Оборудование для производства профилированных страничек конструктивно складывается из металлической, обычно металлической, рамы, силовой установки, набора валов с закреплёнными на них валками. Последние входят в примечательный контакт с обрабатываемым материалом, а потому значительно почаще выходят из строя в результате разных форм износа поверхности, неспециализированного старения материала. Исходя из этого производятся съемными. Валы приводятся в перемещение с помощью пневматического, гидравлического, электромеханического приводов. Огромную мощность разрешает развивать гидравлический привод.
Профилегибочное оборудование с ручным приводом фактически не видится, без оглядки на то, что кое-какие технологические операции, например резка железных страничек, входящие в перечень работ по производству профлиста, металлочерепицы сумеют осуществляться за счет мышечного упрочнения человека.
По своим размерам станки так же очень различаются, в зависимости от целей их применения (например, станок для выпуска железной черепицы не занимает площадь в один квадратный метр, тогда как стан по профилированию листовой стали может только в длину достигать 10-12 метров). Разглядим элементы конструкции более тщательно.
Валки и валы
Основной рабочий инструмент профилегибочного стана. Как отмечалось выше, валки делаются съемными. На валу предвидено пара фиксированных позиций для валков (обычно, до 16), с шагом порядка восемьдесят мм. Валки сумеют устанавливаться в произвольном количестве, на произвольном расстоянии друг от друга (но обязательно кратному наименьшему шагу). Заготовка (тонкий железный лист) пропускается через набор поочередно установленных друг за втором валов, называемых клетями. В станке устанавливается от восемь до 20 четыре клетей.
Такое огромное количество нужно для постепенного профилирования заготовки. Если попробовать придать ей нужную форму за один проход, то неизбежно происхождение повреждений, разрывов. Чем больше клетей, тем выше возможно гофр. В современном постройке огромнейшее распространение забрали странички с высотой профиля от восемь до 100 10 мм. Чем выше профиль, тем наименьшая ширина будет у выходного странички.
Заготовка имеет толщину от 0,45 до 1,2 мм, без оглядки на то, что в последовательности случаев может потребоваться и лист шириной не более 0,31 мм, либо более 1,5 мм. Изменение толщины обрабатываемого материала просит изменение зазора меж валками профилегибочного стана. Один тот же станок может употребляться для обработки материалов разной толщины, но, в большинстве случаев, с отличием не более чем в 0,2..0,3 мм.
Высочайшие требования предъявляются к состоянию и качеству обработки поверхности валков, которая вступает в примечательный контакт с материалом обрабатываемой заготовки, а потому каждые выступы, сколы, царапинки безизбежно приведут к повреждению поверхностного слоя материала грядущего изделия, что неприемлимо. Потому что повреждается не сталь, а ее антикоррозионное покрытие — цинк (шириной всего в 0,02 мм), полимерная пленка, либо краска. Это очень не потрясающе отражается на сроках работы изделия, понижая их до нескольких раз.
Исходя из этого валки подвергается очень кропотливой обработке и проверке, контролю в период эксплуатации. Срок их работы оценивается в 1,5-2 года. Также учитываются повреждения, вызванные смятием. На выбор типа материала рабочего органа, и способ обработки его поверхности оказывает существенное воздействие и вид обрабатываемого материала (пластик, покрытыя цинком сталь, алюминий).
Что касается валов, то они выходят из строя по событию скопления усталостных разрушений, возникновение которых провоцируется бессчетными циклами повторно-переменного нагружения и скручивания. Требования к чистоте обработки их поверхности не столь твёрды. Нижние валы делают несущую и поддерживающую роли для заготовки.
Привод
Оборудование для профлиста значительно почаще оснащается гидравлическим приводом, конструктивно складывающимся из набора гидравлических моторов, совокупы трубопроводов и шлангов, арматуры и вспомогательного оборудования (масляных фильтров, гидронасосов и т.п.).
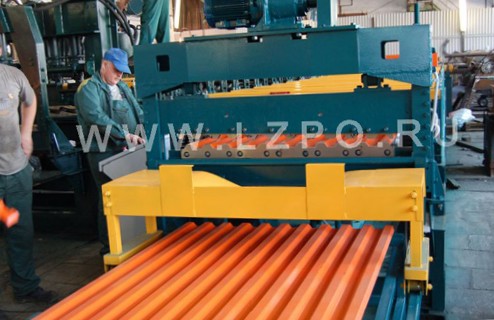
Внедрение в конструкции привода разрешает заавтоматизировать его работу, включить в состав автоматической технологической полосы по производству профилированных железных страничек, в рамках которой роль человека сводится только к контрольным функциям, настройке и перенастройке на выпуск нового типа изделий.
Основной недочёт гидравлического привода — это возможность происхождения протечек рабочей воды (то же самое справедливо и для пневматического привода). Обычно, гидросистемы употребляются в огромных станках, на которых делается профилированный настил и где требуется развитие большого упрочнения. При изготовлении массы дополнительных частей часто употребляется оборудование с электромеханическим приводом.
Оборудование для металлочерепицы, еще 1-го широко всераспространенного строительного материала, подобно оборудованию для производства железного настила. Не считая непосредственно профилегибочного стана и тут, и в том месте употребляются отрезные устройства (гильотины для поперечной резки и ножи роликового типа — для продольной), разматыватели рулонов листового металла (консольного либо портального типа), приемные устройства (рольганги), компьютеризированная совокупа автоматизации производства.
Железная черепица выпускается из того же сырья, что и профнастил, отличаясь от него только формой профиля, размерами готового изделия, что накладывает отпечаток на разработку производства. Требования к их состоянию и станкам монотонны, что при изготовлении черепицы, что сайдинга.
Комментариев пока нет, добавьте свой!